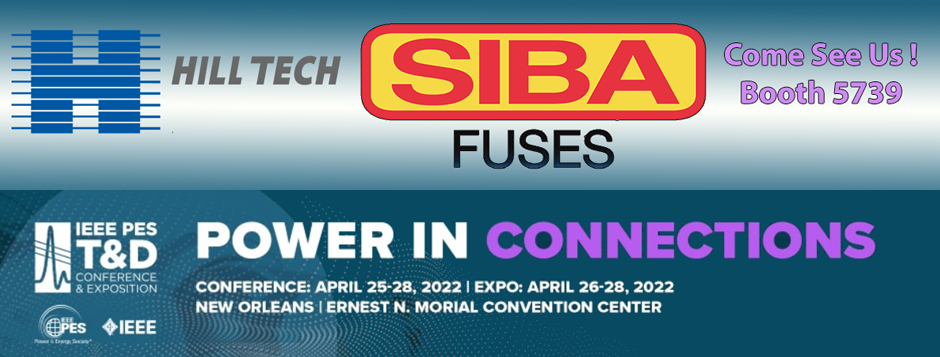
Released April 7, 2022 – Palatine, IL – Hill Tech Headquarters
SIBA FUSES is the world’s leader in protection technology. They offer unmatched electrical protection for energy professionals. Come see how SIBA and Hill Tech innovations for Energy Storage and MV Fuses (Medium Voltage) applications. SIBA’s inventions are driving change in the industry enabling you to respond to current and future electrical protection challenges. The exposition is held at the Orleans Ernest N. Morial Convention Center, April 26-28, 2022. See SIBA booth 5739.
We are ready to assist you at our booth providing a comprehensive technical staff knowable in IEEE’s esteemed standards. Our product display showcases the widest innovation in T&D solutions. Our products cover Energy Storage, Medium Voltage Transformer Protection, Medium Voltage Capacitor Banks, PV Fuses, Switch Gear, and other protection applications.
According to Andrew Hill, President of Hill Tech Sales “More than ever engineers appreciate the value of meeting face with other knowledgeable engineers to explain the challenges they face. The solutions that are a direct result of these interactions are invaluable”.
Since the exposition is held just once every two years it is important to attend this year. The IEEE PES T&D Conference & Exposition is the world’s largest. The forum shares the latest technological developments in the electric power industry. Please don’t miss out on SIBA and Hill Tech innovations for Energy Storage and MV Fuses (Medium Voltage).
For additional assistance, contact us at 847-255-4400 or sales@hilltech.com. You can submit a request for a quote directly by using our automated request system.
Make sure to take this opportunity, to see SIBA FUSE at booth 5739. If you are unable to attend the expo please see our website for the latest information.